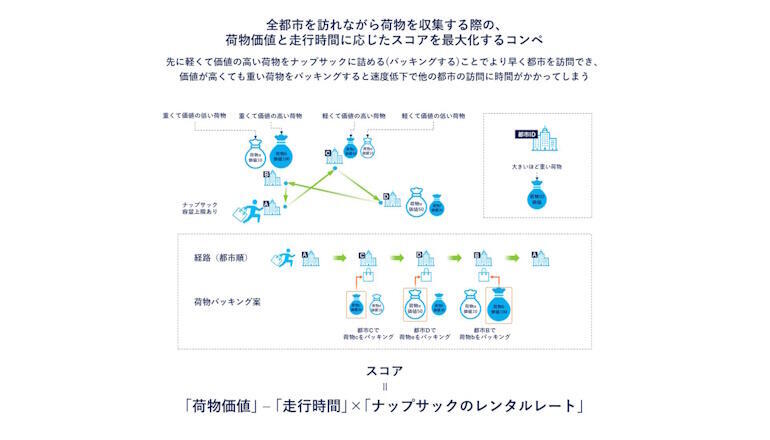
生産計画の立案時間を削減する"単目的最適化技術"を保有し、複数製品の切り替え作業時間を最小にする、各製品の生産順序の並び替え等に活かしてきた。多品種少量生産や、急な市場変動要因による柔軟な計画変更等のニーズの高まりを受け、このような技術はより重要になる。
実際の現場では切り替え時間のみならず、複数のファクターを考慮した生産計画立案が求められる場合がある。従来手法では、切り替え時間最小化アルゴリズムに、生産優先順位の遵守アルゴリズムをプログラミングにより追加実装する必要があり、当該プログラミングにかかる時間が大きな問題になっていたという。パナソニックコネクトは、データ規模に応じて適切にアルゴリズムを自動選択する「多目的最適化技術」を開発し、世界コンペで2位となった。
進化計算のトップカンファレンスGECCO 2024のTTPコンペティションにて、巡回セールスマン問題とナップサック問題との組合わせを前提とし、全ての都市を訪れて荷物を収集する際の、都市訪問時間の最小化と荷物価値の最大化を同時に行うタスクに取り組み、10分間で回答し、第2位の評価を獲得した。
既存手法(GitHub)をベースとし、昨年豪州CSIRO他により報告された走行時間・荷物価値の協調探索手法CoCoアルゴリズムを用いた。計算手法の見直しを行い、都市数100~120の問題には網羅的に経路と荷物パッキング案を探索できる局所探索手法を、都市数が中規模・大規模の場合にはCoCoを導入した。
サプライチェーン領域、製造・物流・流通現場で、複数の制約条件下でも短時間で最適解を算出し、かつ現場ごとに異なる制約条件への対応スピードの加速が図れるようになる。同技術により、計画立案業務に対する大幅な工数削減を実現することで、最適な計画の無い現場で発生する多様な業務から人々を解放し、人が一層創造的な業務に時間を割くことを可能にするという。