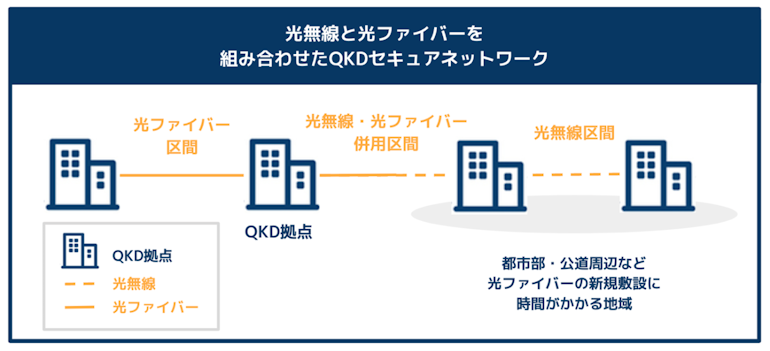
見比べながらの作業では抜け漏れが生じやすかったり、所要時間が経験に左右されたりする。様々な課題に対して、その自動車メーカーは働き方改革を通して業務効率化の検討を進めてきた。その一環で、車両や車両用部品と、図面やガバリとを比較する業務の改善を進めている。作業性向上に資する先進的なデジタル技術を取り入れていて、今回さらなる効果を期待しているという。
日産自動車の協力を得て、新たなしくみを開発した、東芝デジタルソリューションズは今月21日、製造現場の3D CADデータ活用ソリューション「Meister MR Link」の提供を開始した。同ソリューションはMR(複合現実)技術と3D CADデータを用いて、物理空間の実物に仮想空間の3Dモデルを重ね合わせて表示する。専用設備が不要で、市販の汎用タブレットを利用して手軽・即かつ安くMRを導入できるという。
設計と実物の差異や品質を確認する作業の効率化に貢献する。データ変換ツールとタブレットアプリで構成され、サブスク型サービスのため初期投資も抑えられる。既存の3D CADデータをMR用の3Dモデルデータに変換し、手軽に現場に持ち込むことが可能となる。作業結果や進捗状況を可視化して、作業の抜け漏れや手戻りの削減に役立てられる。
同ソリューションの導入により、ガバリ自体が不要になり、試作車両の実物に3Dモデルと打点データを表示し、打点品質をチェック・実績登録する一連の作業がタブレットで行える。現場での完結事項が増え、レポート作成など事務処理時間を削減できる。実際、最大8割の時間削減に成功した事例があるという。