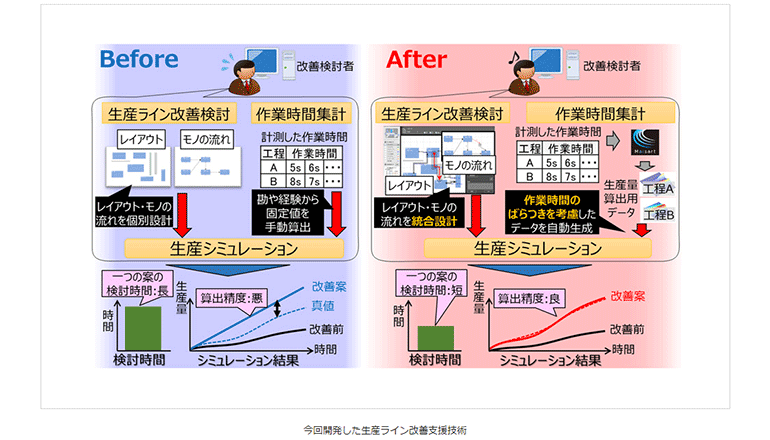
ものづくりをする生産ライン。そこでは製造装置や棚などのレイアウトとモノ(製品)の流れの最適化が求められる。それらは従来、個別に設計されていたので、実際に組み合わせると、必要な作業エリアが抜けていたり、工程間に長い経路ができていたり、工程間の経路が交差していたり――。
問題が発生すればその修正に手間がかかるうえ、複数の改善案の比較検討に必要となる生産量は、勘や経験に基づいて算出されていたために、作業時間のばらつきや時間帯ごとの作業効率の変化が大きく、高精度化が困難。高い精度を求めてシミュレーターを利用する場合には、それらの変化を踏まえた生産ラインのモノの流れと各工程の時間の設定に多くの労力が費やされていたという。
三菱電機は、生産現場の改善活動を効率化する『生産ライン改善支援技術』を開発した。生産ラインのレイアウトとモノの流れの統合設計による設計工数の削減と、同社AI「MaisartⓇ」を用いた生産量算出の高精度化により、改善検討工数を従来の2分の1に削減し、勘や経験に頼らない安定した改善検討を実現し、生産性向上に貢献する。
同技術は、上記統合設計により、個別設計では気づかない矛盾や修正の手間を削減し、生産ラインの改善案を効率よく導出する。レイアウト・モノの流れ、運搬速度などのデータから算出したDI(ディスタンス・インテンシティ)分析結果など、生産ラインの良否判断に用いる情報を分かりやすく可視化し、改善検討作業の質を向上する。
生産ラインの各工程で計測した作業時間から、AIを用いて時間のばらつきや時間帯による作業効率の変化を分析し、生産量算出用データを生成。このデータにより、改善案における生産量を90%以上の精度で算出する。生成したデータと設計したレイアウト・モノの流れをシミュレーターに自動反映することで、シミュレーターの設定を自動化し、複数の改善案の比較検討作業を効率化するという。