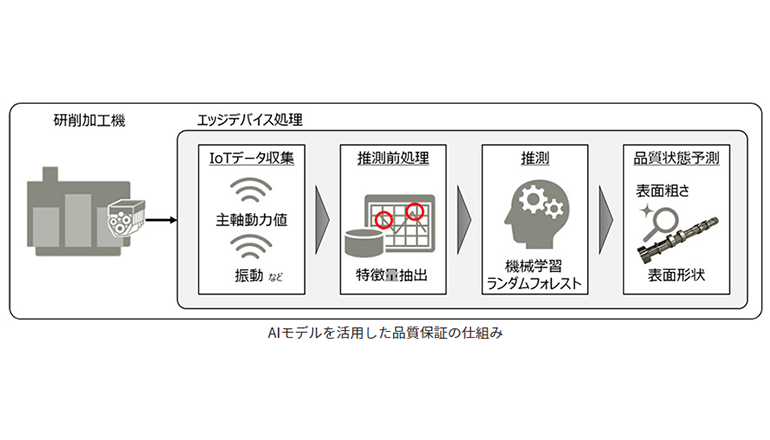
1.世界シェアの強み、良質なデータを活かしたニーズ特化型サービスの提供。2.第四次産業革命下の重要部素材における世界シェアの獲得。3.新たな時代において必要となるスキル人材の確保と組織作り。4.技能のデジタル化と徹底的な省力化の実施。
我が国製造業が今後も競争力を維持・強化するための具体的な方策として、上記4点が経産省・厚労省・文科省の共同執筆による「ものづくり白書」で提起されている。昨今この国の実態として、さまざまなメーカーでは、生産現場の最適化を実現するため、IoTやAIを活用したスマート工場化が進む一方で、どのように生産性とコストを犠牲にすることなく品質を向上させるかが課題になっているという。
富士通とSUBARUは4日、エンジン部品加工工程における研削加工の品質保証を向上させる、高精度に加工品質を判断するAIモデルを活用した実証実験を、SUBARU群馬製作所大泉工場の量産ラインで開始する。同モデルは、カムシャフト研削工程において研削設備に接続したセンサーから主軸動力値や振動のデータを収集・分析し、加工中の全カムシャフトの品質をリアルタイムに推測するもので、両社が共同開発したという。
今回の実証実験では、収集したセンシングデータからAIモデルが推測した加工時の品質状態と、実測値とを照合し、正確性を測ることで、加工後の全カムシャフトの品質保証が可能となるかを検証する。また、研削砥石の表面を研いで切れ味を取り戻すドレッシング作業において定期交換していた研削設備の消耗部品を、品質基準を順守しながら極限まで活用すること(ドレッシング間隔を延伸)の可能性もあわせて検証していく。
来年1月31日まで行う上記実験の成果をもとに、両社は、AIモデル活用による品質保証システムの量産ラインへの本格適用や、他部品やエンジン工場全体への横展開を推進し、さらなる最適生産・品質向上を目指していく構えだ。