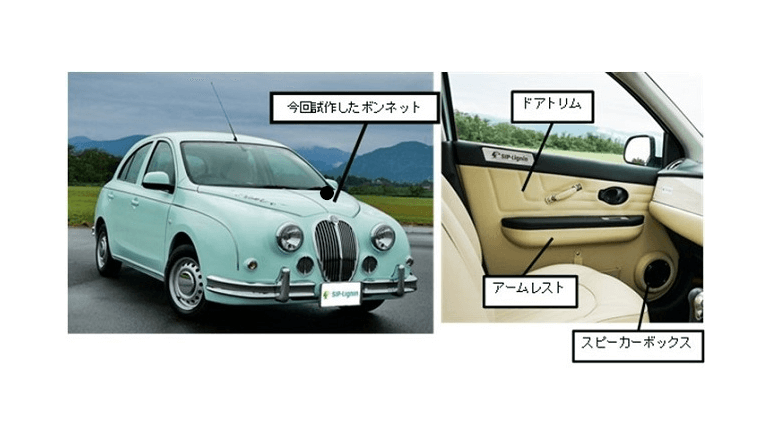
リグニンは木材を構成する主要成分の一つで、木材成分の約3割を占め、化学構造の特徴としては芳香環を含んでいる。芳香環を持つ素材には、耐熱性、難燃性などを発揮する優れた材料となる可能性があるものの、リグニンを利用した材料の本格的な商用化は達成されていない。
紙パルプ製造の副産物としてリグニン系の素材を製造できるが、通常の紙パルプ製造工程では強いアルカリを用いて処理するため、極めて加工性に乏しい素材しか製造できないという課題がある。また、リグニンは植物種により異なった化学構造を持つため、リグニン系素材を安定的に製造するには、植物種を限定することも重要とされている。
改質リグニンをネットワークポリマー化するための液状硬化剤を改質リグニンに加える。この硬化剤は改質リグニンと極めて混合しやすく、揮発性有機溶媒は不要。次に分散媒として、改質リグニンと反応して堅牢にするエポキシ化合物(ビスフェノールA型エポキシ樹脂)を改質リグニンに対し五倍重量加えて均一に混合すると成形樹脂が得られる。成形樹脂を真空含浸法で型に設置したガラス繊維布に含浸させ、乾燥・仮硬化を行った後、型から外して120℃で最終硬化を行った。
改質リグニンは粘性が高く、そのままでは真空含浸できない。粘性を下げるために溶媒を加えると乾燥収縮が起き、十分な寸法精度が得られなかった。また、加熱によって粘性を下げると、樹脂が硬化してしまう問題があった。
今回、溶媒の代わりに液状硬化剤を添加して粘性を下げ、通常よりも高温だが、樹脂の硬化を防げる温度に調節されたオーブン中に型を設置。真空含浸法で、均一に樹脂を含浸させた。作製したサンプルからの揮発性有機溶媒スチレンの発生量を評価したところ、改質リグニンを用いたGFRPの場合は、不飽和ポリエステル樹脂を含浸させる従来品の4500分の一未満であった。また、硬化処理前後の部品の収縮率は従来品と比較して一桁小さくなり、自動車用として十分な寸法精度が確認された。
内装部品としてはドアトリム4枚、スピーカーボックス、アームレストそれぞれ4つを試作し、小型車に取り付けた。自動車外装部品としてはボンネットを試作した。ボンネットについては、強度の他、製品として問題のない外観の塗装ができた。
2018年10月より、これら改質リグニン使用GFRPの実車搭載試験を世界で初めて開始。実車搭載試験では、温度、湿度などの車内環境を自動計測するとともに天候と走行を記録して、部品の経時変化を評価し、実使用上の問題点などを抽出する。
今後は、一年程度をかけて紫外線、温度変化などによる自動車内外装部品の変化をモニターして、長期間、十分実用に耐えるかどうかを確認する。改質リグニンの生産開始が予定される2022年に改質リグニンを用いたGFRP製自動車部品を用いた環境に優しい自動車としてのブランド化を目指す。