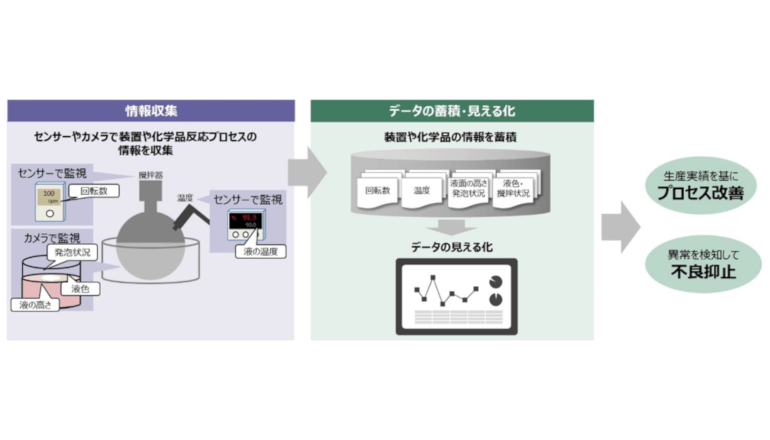
製造業では近年、顧客ニーズの多様化や急速なデジタル化の進展、グローバル競争の激化により顧客の個別要求に応じた多品種少量生産が求められている。
一般的な計装機器を用いたセンシングが困難な小規模の化学品製造工程では、目視による定点的な製造状態の監視をもとに品質管理を行っている。が、液体量や時間などが同一の製造条件下でも完成品の質は異なり、品質安定化のためには攪拌中の液体の発泡状況や色の変化などに表れる多様な要因をもとに品質管理せねばならず、また、生産性の低下につながるので製造監視の頻度を上げることも難しいという。
ダイキン工業と日立製作所は、IoTを活用した協創の第二弾として、化学品製造工程の反応プロセスの品質管理ノウハウのデジタル化に向けた共同実証を10月から開始。ダイキンの淀川製作所内のフッ素化学品製造工程の反応プロセスに、作業者に異常発生や適切な操作タイミングなどをタイムリーに伝えることができるシステムを導入する。
両社は、次世代生産モデルを実現する協創の第一弾として、空調機の製造工程向けに開発した「ろう付け技能訓練支援システム」を、ダイキン滋賀製作所にて昨年10月から運用し、現在、国内外の拠点に導入範囲を拡げている。同システムで活用した日立Lumadaの画像解析技術を、フッ素化学品の製造工程における反応プロセスに適用し、品質管理ノウハウのデジタル化に向けた検証を行ってきたという。
ダイキン淀川製作所では、センサーやカメラを用いて4M(人、設備、材料、方法)の観点で化学品の反応状態(液色、発泡等)や、装置の動作(温度、回転数等)の時系列の数値・画像データを収集。リアルタイムかつ連続のデータにより化学反応状況の見える化を可能にすることで、今後の品質管理の安定化と作業効率改善の実現をめざすという。
今回の協創は18・19日、東京での日立社会イノベーションフォーラムにて披露される。