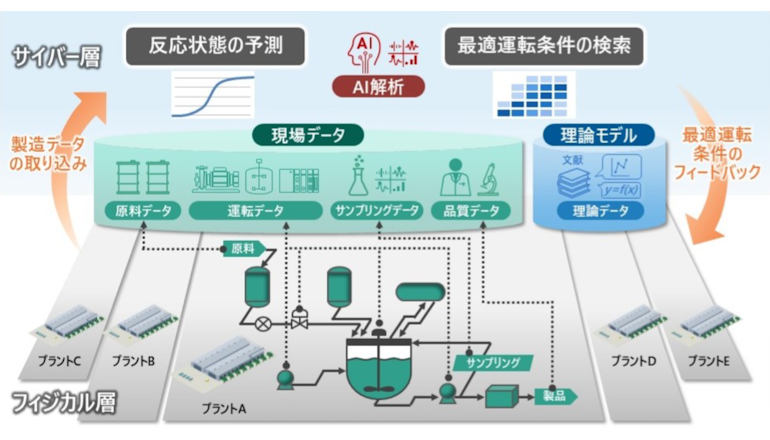
原料投入・製造・製品取出しプロセスを都度実施する、バッチ生産は少量多品種に適する。一般的な合成樹脂のそれにおいては、製品品質を担保するために、人が、反応工程の途中でサンプリングや分析、反応進捗判断を繰り返しつつ調整原料の投入を行う。
反応前工程の温度、圧力などの動向も製品品質に影響を与えるため、全工程にわたる運転状況の把握と考慮が不可欠である。作業は煩雑かつ属人的になる傾向があり、品質検査合格率のばらつき等の課題もあったという。DICと日立は、合成樹脂製造プラントの運転自動化を図るデジタルツイン技術――プロセスインフォマティクス(情報科学技術による製造工程最適化)を活用したシステムを前者の国内プラントで来年1月から本格稼働させる。
これまでの共同実証の結果、製造工程における反応状態の予測および最適運転条件の探索技術を確立し、実用化に至った。国内3拠点と、海外1拠点へ展開予定である。バッチ生産に対応する同システムは、目標品質値を得るための運転条件を自動算出し「ヒートマップ」として明示する。ほかに、「約20回のバッチ生産運転データのみで化学品製造に活用できるモデルの作成」
「システム画面に表示する粘度などの『品質予測カーブ』により、製品品質の推移と反応工程が終わるタイミングを確認」「同カーブは反応終了時点までの品質を予測」「運転実績との比較機能により、作業員が納得感をもって運転条件の確認を行うこと」それぞれが可能といった特長を有する。
上記システムの本格稼働を皮切りに、DICはAI技術の権利化(特許第7388606号、特許第7388607号)をより積極的に進める。日立とともに、高度な自動製造システムの実現をめざし、サプライチェーンを含めた全体最適化・効率化の取り組みも検討していく。一方、日立はLumadaソリューションである同システムを、化学メーカー向けに広く展開もしていく考えだ。