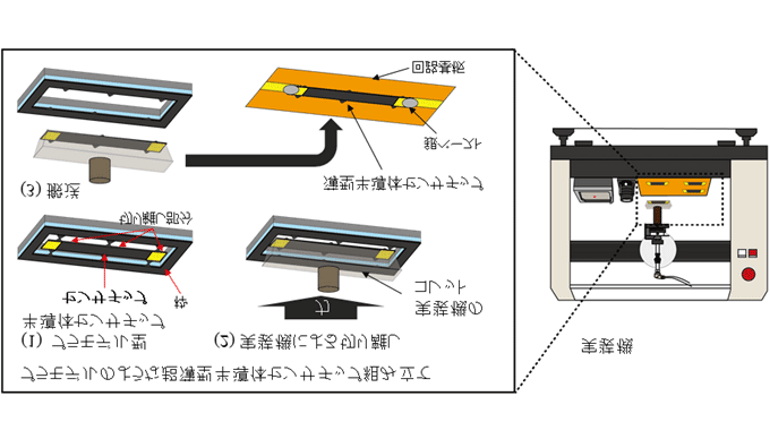
近年、プラスチック上に製造できる有機半導体を用いた屈曲可能な電子機器、有機ELや有機太陽電池のような「フレキシブルエレクトロニクス」が注目されている。一方で、動作速度や安定性の高いシリコンデバイスは、厚くかつ硬いため、その適用が難しいと考えられている。
既存のセンサやアンプ、集積回路などを構成するシリコンを用いた半導体デバイスは、厚みが300μm以上であり、それを非常に薄くしてフレキシブル化することが試みられてきたが、切断や搬送を現在の半導体工場にあるダイシングソー(切断装置)や実装機(精密組立装置)で行うことが難しく、これまで実用化が困難であったという。
東大大学院新領域創成科学研究科と産総研集積マイクロシステム研究センターの研究グループは、一般的な半導体製造プロセスを用いて大量に一括製造した厚さわずか5μmの高感度センサ「超薄型半導体ひずみセンサチップ」を、実装機を用いて、プラモデルのパーツのように1つずつ切り離して回路上に配置配線する技術を開発。切り離し部分に力が集中し、センサや集積回路部分には力がかからない構造の設計方法を確立した。
同センサチップの構造は、周りの枠と細い切り離し部でつながったプラモデルと同様の形状である。センサチップは壊れないが切り離し部分だけ切断されるように機械構造設計を行い、同時に開発した精密組立技術によって、プラモデルのようにセンサチップを切り離して電子回路上に貼ることに成功したという。研究は、新エネルギー・産業技術総合開発機構の委託事業として実施された。
そしてその成果が英国科学誌サイエンティフィック・リポーツ電子版に掲載された。今回の手法は、ウェアラブルデバイスやスマートウォッチのセンサ、集積回路などが入った硬い半導体部分を超薄型にして柔らかくすることを可能とする技術であり、次世代高性能フレキシブルエレクトロニクス実現への貢献が期待されるという。